4 Elements that every SOPs must have to be effective
- Aldo Arecco
- Mar 8, 2022
- 2 min read
When I join the Navy in my country one of the things I realize was how almost every part of the routine and daily work was structured in a way that even a young seaman can understand. From daily cleaning to equipment and engines maintenance, procedures and standards were already established so they were easy to follow even in a situation that can be complicated like equipment malfunction, combat exercises, bad weather, etc.
Later time, while working for a wholesale and retail company, I could feel how regular functions like procuring, sales estimations, logistics, and customer service can become chaotic if the service processes change from time to time and there are no established standards. When a business with more than 50 people still is run like a Mom and Pop, things can become chaotic anytime. Owners do not have a business but work full time on their business. This is the time when problems like frustration, lack of trust, micromanaging, slow reaction and high rotation take a big leap on the business growth and it gets stuck.

Achieving simplicity o the business may bring the following benefits:
Clarifies the process
Documents the best way to do a job
Ensures operating consistency
Expedites employee training
Provides the baselines for improvement
In order to start working on creating an effective way to work that can keep the team motivated and well organized we need to set up the right Standard Operational Procedures(SOPs)
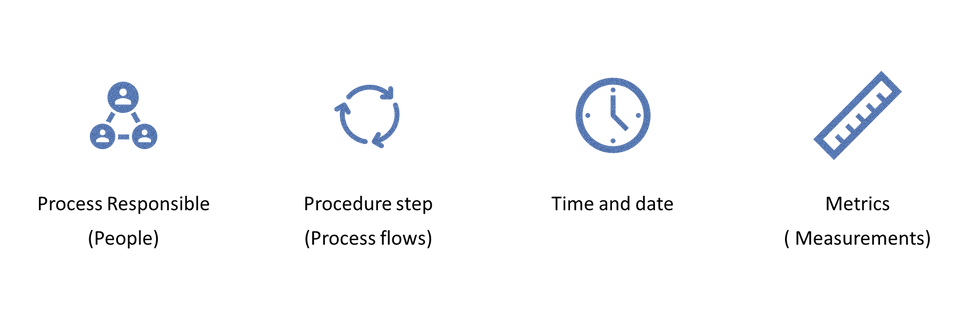
PROCESS RESPONSIBLE: The first thing we need to define about every SOP is WHO owned the process. what Area is responsible and team members with their specific roles in every step. It might be useful to have codification,
PROCEDURE STEP: A comprehensive description of the procedure considering all the equipment and material involved to perform the work. Also should provide ways to verify the work was done correctly and safety precautions,
TIME AND DATE: SOPs are required to have a description of when the work should be performed including any predecessor o verification to be done previously specifying time, that needs to be registered and signed by the team member.
METRICS: If there are no metrics there is no way to validate the work has met the specific standards provided. Also, any specific number or indicator that is relevant for the equipment or service that is being performed must be registered, This will provide a way to measure how well or bad we are doing.
These four elements of course there are NOT the only ones that can be included. Usually, SOPs included references to quality standards, safety rules, coding or color classification, etc. The important thing is to understand how these procedures and standards will reduce ambiguity and ensure that the work is performed correctly and most importantly with Safety.
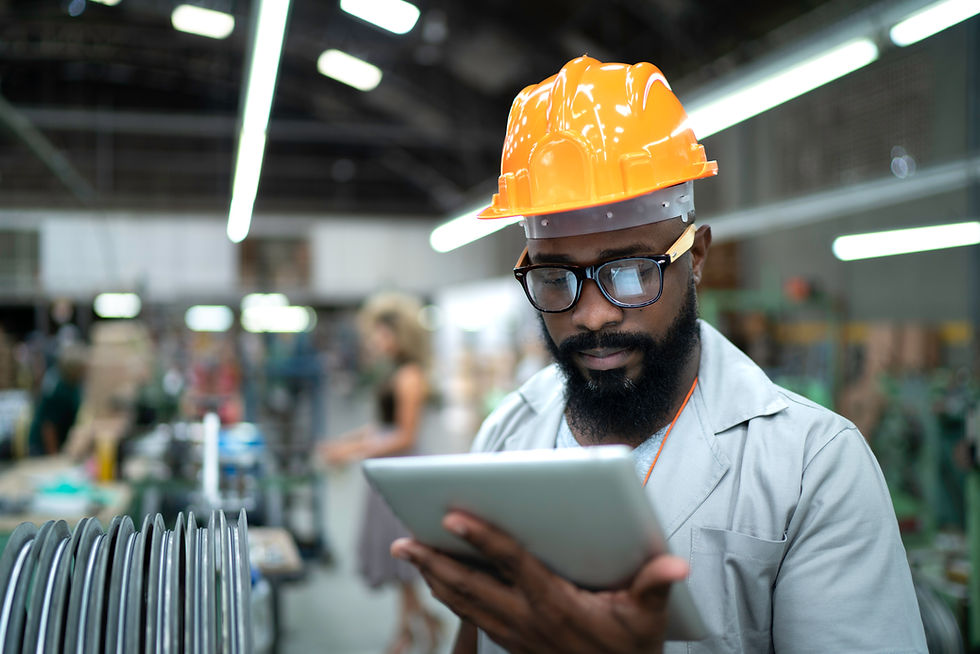
Comments